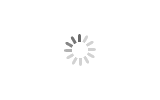
GOMIN 800°C-1200°C high-temperature resistant series
The GM series high-temp ceramic coatings feature: 1) Outstanding heat resistance (600-1200°C long-term, 1280°C peak); 2) Hybrid tech with siloxane/polysilazane matrix and nano-fillers for dense protection; 3) Multi-defense against chemical corrosion, water, UV and mechanical stress; 4) Broad industrial use in petrochemicals, power and metallurgy. Engineered for extreme durability through nano-ceramic technology.
Product Features
1. GM-812 Ceramic Anti-Corrosion Coating
Film-Forming Material: Inorganic-organic modified siloxane (---Si---O---Si---) with modified flake-shaped high-temperature resistant pigments and fillers.
Temperature Resistance: Cures at room or low temperature; coating withstands up to 1200°C and can endure 800°C rapid thermal shocks.
Corrosion Resistance: Resistant to high-temperature acids, alkalis, salt solutions, and corrosive gases; waterproof, UV-resistant, and thermal shock-resistant.
Curing Mechanism: Dual-action curing (moisture evaporation + curing agent), forming an inorganic network structure for dense anti-corrosion protection.
Applications: High-temperature equipment in petrochemical plants, flue gas ducts, chemical acid/alkali tanks, and anti-corrosion for coke oven gas in steel mills.
2.GM-1012 1200°C High-Temperature Sealing Coating
Film-Forming Material: Inorganic-organic silicone resin with nano-graphite flakes, alumina, and rare-earth powders.
Temperature Resistance: Long-term resistance to 1200°C, with oxidation resistance, waterproof sealing, and high thermal expansion coefficient.
Protection Mechanism: Multi-layered graphite flake sealing structure extends medium penetration paths.
Applications: Heating boiler inner pipes, high-temperature waterproof/damp-proof substrates, and acid/alkali corrosion-resistant environments.
3.GM-1060 High-Temperature Anti-Corrosion Nano-Ceramic Coating
Film-Forming Material: Polysilazane with sericite powder, chromium black powder, and phosphates.
Temperature Resistance: Long-term resistance to 600°C, short-term peak at 1000°C, and thermal shock resistance (600°C-to-water quenching).
Mechanical Properties: Forms covalent bonds with substrates after curing, resulting in a dense, defect-free coating.
Applications: Boiler components, pipelines, metallurgical equipment, electric heating elements, and high-temperature chemical parts.
4.GM-1280 High-Temperature Anti-Corrosion Nano-Ceramic Coating
Film-Forming Material: Polysilazane with sericite powder, chromium black powder, and phosphates.
Temperature Resistance: Long-term resistance to 800°C, short-term peak at 1280°C, and thermal shock resistance (600°C-to-water quenching).
Mechanical Properties: Covalent bonding with substrates ensures a dense, defect-free coating.
Applications: Boiler components, pipelines, metallurgical equipment, electric heating elements, and high-temperature chemical parts.
Performance Parameters
Product Model | Key Specifications | Test Standards |
GM-812 | Adhesion: 6MPa | GB/T 5210-2006 |
GM-1012 | Adhesion: Grade 1 | GB/T 9286-1998 |
GM-1060 | Adhesion: Grade 0 | GB/T 10125-1997 |
GM-1280 | Adhesion: Grade 0 | GB/T 10125-1997 |
Application Instructions
▊ Surface Preparation
General Requirements: Ensure surfaces are clean, dry, and free from dust, oil, and rust.
Specific Requirements:
GM-812/GM-1012: Abrade to a roughness of 25-40μm (St3 or Sa2.5 grade).
GM-1060/GM-1280: Sandblast to Sa2.5 or abrade to St3 grade.
▊ Application Methods
Spraying: Air spraying (recommended large-nozzle spray gun for GM-812/GM-1012).
Brushing: Cross-brushing method (universal).
▊ Drying&Curing Conditions
GM-812:Surface dry: ≤30min,Full cure: ≤24h (at room temperature)
GM-1012:Surface dry: ≤2h,Full cure: ≤24h
GM-1060/GM-1280:Cure at 180-200°C for 1-1.5 hours.
▊ Thinners
GM-812/GM-1012:Deionized water (GM-812)
Xylene/acetone (GM-1012)
GM-1060/GM-1280:Alkanes, esters, ethers
Packaging & Storage
Product Model | Packaging Specification | Storage Conditions | Shelf Life |
GM-812 | 10kg/drum (steel drum) | Dry & cool (0°C-40°C) | 12 months |
GM-1012 | 10kg/drum (steel drum) | Dry & cool (0°C-40°C) | 12 months |
GM-1060/GM-1280 | 10kg/drum (steel drum) | Dry & cool (5°C-30°C) | 6 months |
Safety Precautions
General Requirements:
Ventilation: Must be applied in well-ventilated areas to avoid inhaling paint mist.
PPE: Operators must wear protective gear (gloves, goggles, masks, coveralls).
Skin Contact: Rinse immediately with soap and water; use specialized cleaner if needed.
Eye Contact: Flush with copious water for ≥15 minutes and seek medical attention.
Qualified Personnel: Only trained professionals should operate, ensuring proper equipment and procedures.
Product-Specific Guidelines:
1.GM-812 Ceramic Anti-Corrosion Coating
Seal unused paint tightly; secure inner plastic bag in drum.
Do not reuse mixed paint—dispose per local regulations.
Expired products require retesting before use.
2.GM-1012 1200°C High-Temperature Sealing Coating
Clean tools thoroughly post-use to prevent curing blockages.
Mixed paint must be used within 4 hours; non-recyclable.
3.GM-1060/GM-1280 Nano-Ceramic Coatings
Mixed paint must be used within 12 hours to prevent tool hardening.
Dry film thickness: 25±5μm (GM-1060) or as designed—excess affects performance.
Critical: Cure strictly at 180-200°C; deviation compromises coating properties.