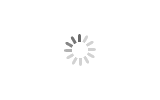
GM-Ⅰ-Ⅱ-Ⅲ Special Anti-Corrosion Series
The GM series offers exceptional corrosion resistance: GM-Ⅰ withstands harsh chemicals (6+ years), impacts/bending, and extreme temperatures (-40℃~150℃), with 100% closed-cell eco-safe formula. GM-Ⅱ, designed for color steel tiles, features UV resistance, anti-yellowing, and easy application. GM-Ⅲ utilizes advanced technology to prevent yellowing (500h fade-free), combining aesthetics with durability. All variants are solvent-free, potable-water-certified, ideal for chemical, marine, and municipal applications.
Product Series Features
1. GM-Type I-001 Special Anti-Corrosion Coating
Key Features:Exceptional corrosion resistance, outstanding physical properties, environmentally safe.Long-term r
esistance to strong acids (5%-50% sulfuric acid), strong alkalis (saturated Ca(OH)₂), salts, and solvents, with anti-corrosion effectiveness lasting over 6 years.High impact resistance (50 kg/cm²), excellent flexibility (no cracks on a ∅10mm mandrel), and broad temperature tolerance (-40°C to 150°C).Solvent-free, passes potable water safety tests, 100% closed-cell structure.
Applications:Storage tanks, pipelines, bridges, offshore platforms, wastewater tanks, and other highly corrosive environments.
2.GM-Type II-002 Color Steel Tile Renewal Anti-Corrosion Coating
Key Features:Anti-yellowing design, easy application, strong weather resistance.High-temperature resistance (120°C), low-temperature resistance (-30°C), 100% closed-cell structure.Superior UV aging resistance, significantly improved color stability.Suitable for large flat substrates (e.g., color steel tiles), can be applied directly or used in combination with Type I.
Applications:Color steel tile renewal, steel structure factories, storage tanks, chemical equipment, etc.
3. GM-Type III-003 Special Anti-Yellowing Anti-Corrosion Coating
Key Features:Upgraded anti-yellowing performance, utilizing international technology to prevent coating discoloration (0-level chalking after 500h artificial aging test).Composite anti-corrosion system, requires Type I as a primer, balances corrosion resistance and aesthetics.Chemical resistance: withstands 50% sulfuric acid, 10% hydrochloric acid, 10% NaOH, etc.; passes 500h neutral salt spray test without rust.
Applications:Marine engineering, municipal facilities, food & pharmaceutical equipment, and other scenarios requiring high color stability.
Performance Parameter Comparison
Test Item | GM-Type I-001 | GM-Type II-002 | GM-Type III-003 |
Acid/Alkali Resistance | No change after 30-day immersion | No change after 30-day immersion | No change after 7-day immersion |
Temperature Range | -40°C ~ 150°C | -30°C ~ 120°C | -30°C ~ 120°C |
Adhesion | 12 MPa (Pull-off) | Grade 1 (Circular Cut) | 10 MPa (Pull-off) |
Impact Resistance | No cracks at 50 kg/cm² | No cracks at 50 kg/cm² | No cracking at 50 cm |
Yellowing/Aging Resistance | Grade 2 discoloration after 168h UV | Grade 0 chalking after 160h UV | Grade 0 discoloration after 500h UV |
Closed-Cell Rate | 100% | 100% | 100% |
*The above data are based on actual formulations and products.
Construction Guidelines
▊ Surface Preparation
Clean the substrate thoroughly to remove oil, grease, and rust; ensure it is dry (moisture content ≤ 8%).For cement substrates, repair any cracks. For metal substrates, sandblasting or grinding is recommended.
▊ Coating Preparation
Mix evenly using an electric stirrer and let stand for 10-15 minutes.For Type III, apply Type I primer first (allow 24-hour drying interval).
▊ Application Methods
Apply by brush, roller, or spray, with a single-layer thickness of 0.1-0.2 mm and a total thickness of 0.3-0.5 mm.Allow a 24-hour interval between coats (at room temperature, 25℃).
▊ Environmental Requirements
Temperature: 5°C–35°C, humidity ≤ 85%.Avoid application during rain or snow.
Precautions
(1) Wear protective gloves, masks, and goggles during application, and ensure adequate ventilation.
(2) After construction, promptly clean tools with dedicated thinner to prevent coating solidification.
(3) Use protective equipment such as gloves, masks, and goggles during application.
(4) Maintain proper ventilation at the worksite to avoid inhaling harmful fumes.
Storage & Transportation
Item | Requirement |
Storage Condition | Store in a cool, dry, and well-ventilated area, away from direct sunlight and high temperatures |
Storage Temperature | Maintain between 5°C–35°C; avoid freezing |
Shelf Life | 12 months (unopened) |
Transport Condition | Avoid severe vibration and impact to prevent package damage |