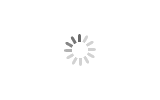
GM-JG UV Coil Coating
UV-cured, ≤3s curing, high-speed production. Eco-friendly, VOC<50g/L, RoHS/REACH compliant. High hardness (≥3H), wear/weather resistant (QUV 1000hrs). Chemical-resistant (acid/alkali/salt). Custom finishes (matte/glossy/metallic). Compatible with steel, GI/GL, Al, etc. For construction, appliances, furniture, industrial parts. Efficient & sustainable.
Product Characteristics
UV coil coating is a high-performance, environmentally friendly paint based on ultraviolet (UV) curing technology, specifically designed for coil-coated metals (continuously coated metal coils). The product achieves rapid curing through UV light initiation, offering advantages such as high energy efficiency, low VOC emissions, excellent weather resistance, and decorative appeal. It is suitable for high-speed industrial coating production lines.UV-triggered curing, with single-layer curing time ≤3 seconds, significantly improving production efficiency.Free of organic solvents, VOC content <50 g/L, compliant with international environmental standards (e.g., RoHS, REACH).High hardness (≥3H, pencil hardness) and wear resistance.Strong weather resistance (QUV 1000 hours without chalking or discoloration).Chemical corrosion resistance (resistant to acids, alkalis, and salt spray).Customizable matte, glossy, metallic finishes, and support for tailored colors and textures.Compatible with various substrates and pretreatment processes (e.g., passivated, phosphated substrates).
Applications
Construction sector (color-coated steel sheets, metal roofing, exterior wall panels, etc.).Home appliance industry (metal casings for refrigerators, washing machines, air conditioners, etc.).Furniture and decoration (metal furniture, indoor/outdoor decorative panels).Industrial components (containers, automotive parts, electronic equipment casings).
Coating Compatibility
Metal substrates include cold-rolled steel, galvanized steel (GI), galvalume steel (GL), aluminum alloy sheets, stainless steel sheets, etc.
Performance Parameters
Item | Parameter Value | Test Standard |
Solid Content | ≥95% | GB/T 1725-2007 |
Curing Energy | 300–600 mJ/cm² (UV-A band) | ASTM D5898 |
Hardness (Pencil Hardness) | ≥3H | GB/T 6739-2006 |
Adhesion (Cross-cut Test) | 0 Grade (No peeling) | ISO 2409 |
Salt Spray Resistance | ≥500 hours (no rust) | ASTM B117 |
Weather Resistance (QUV accelerated aging) | 1000 hours (no chalking, ΔE≤2) | ASTM G154 |
Chemical Resistance (24h immersion) | 10% H2SO₄, 10% NaOH (no abnormalities) | GB/T 9274-1988 |
Application Instructions
▊ Substrate Pretreatment
Cleaning: Remove surface oil and dust (recommended: degreaser + water rinse).
Chemical Treatment: Apply phosphating/passivation to enhance adhesion.
Drying: Substrate moisture content <5%, temperature ≤50°C.
▊ Coating Parameters
Application Method | Roll coating (recommended), spray coating, or curtain coating |
Film Thickness Control | Wet film: 10–20 μm / Dry film: 8–15 μm |
UV Curing Conditions (Wavelength) | 320–400 nm (medium-pressure mercury lamp recommended) |
Energy Density | 300-600 mJ/cm² |
Conveyor Speed | 10–30 m/min (adjust based on lamp intensity) |
▊ Recoating & Intercoat Interval
Wet-on-wet multilayer coating is applicable without interlayer curing.
If recoating on a cured layer is required, sanding and surface cleaning are necessary.
Precautions
(1)Store in light-proof and sealed condition (5-35°C), shelf life 6 months, keep away from fire sources, avoid freezing or high temperature. Temperature: 20-30°C, humidity <70%. Prevent dust contamination, ensure clean coating workshop.
(2)Operators must wear safety goggles, UV-protective face shields, and gloves.
(3)In case of skin contact, rinse immediately with soap and water. If swallowed, seek medical attention immediately.
(4)Incomplete Curing: Inspect UV lamp intensity, conveyor speed, or coating formulation.
(5)Coating defects (orange peel, pinholes): Adjust roll coating pressure and clean coating rollers.