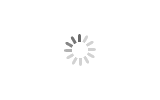
GM-201High-Temperature Resistant Anti-Corrosion Nano-Ceramic Coating
This product utilizes polysilazane as the film-forming substance, combined with high-emissivity functional fillers (such as silicon carbide, zirconium oxide, etc.), copper-chromium black powder, and inorganic composite powders, forming an organic-inorganic hybrid system.
Product Characteristics
This product utilizes polysilazane as the film-forming substance, combined with high-emissivity functional fillers (such as silicon carbide, zirconium oxide, etc.), copper-chromium black powder, and inorganic composite powders, forming an organic-inorganic hybrid system. The coating can withstand temperatures exceeding 1000°C, exhibiting high-efficiency thermal radiation performance (emissivity ≥ 0.85), excellent corrosion resistance, high hardness, and thermal shock resistance. The cured coating is dense and bonds with the substrate through chemical bonds, significantly enhancing mechanical strength and thermal radiation efficiency. It is suitable for scenarios requiring rapid heat dissipation or optimized thermal management.
Applications:Industrial furnace linings, high-temperature pipelines, and heat exchanger surfaces.Power equipment heat dissipation components, engine exhaust systems.Metallurgical equipment, casting molds, and high-temperature sensors.Solar collectors, infrared heating elements.Chemical reaction vessels, high-temperature storage tanks, and heat dissipation coatings.Aerospace high-temperature component thermal protection systems.
Coating Applicability:Carbon steel, stainless steel, high-temperature alloy steel, titanium alloy, ceramics, glass-ceramics, and other high-temperature resistant materials. (Note: Substrate types require matching with specialized formulations, and specific working conditions can be customized and adjusted.)
Performance Parameters
1. Core Thermal Radiation Performance
Thermal Emissivity(ε) | ≥0.85(GB/T 13477-2017) |
Thermal Reflectance | ≥80%(ASTM C1371) |
Thermal Shock Resistance | No cracking after 50 cycles of 600°C ↔ room temperature |
Thermal Efficiency Improvement | Coating improves surface heat dissipation efficiency by 20%-30% (laboratory tested) |
2. Coating Performance Data
Parameter | Test Standard | Performance |
Condition in Container | Visual Inspection | Uniform, no lumps, no sedimentation |
Mixed Color | Visual Inspection | Dark gray (customizable) |
Adhesion | GB/T 9286-1998 | Grade 0 |
Coating Hardness | GB/T 6739-2006 | ≥5H |
Neutral Salt Spray Resistance | GB/T 10125-2021 | No rust or blistering after 30 days |
High-Temperature Oxidation Resistance | GB/T 13303-2020 | Weight loss rate <1% after 100h at 800°C |
Thermal Emissivity (ε) | GB/T 13477-2017 | ≥0.85 |
Application Instructions
1. Process Description
(1)Substrate Pre-treatment:Sandblasting (Sa2.5 grade) → Degreasing and cleaning → Drying.
(2)Coating Preparation:Mix A:B in a ratio of 2.5:1.Filter through a 120-mesh sieve.Allow to stand for deaeration.
(3)Coating Application:Spray coating (recommended 1.0 nozzle spray gun) → Surface drying (10 minutes) → Curing (250°C/1 hour).
(4)Quality Inspection Requirements:Dry film thickness ≤30μm.Ensure uniform coating without missed spots.
2. Precautions
(1)The thermal radiation performance of the coating changes non-linearly with increasing film thickness. It is recommended to apply a single coat to avoid excessive thickness.
(2)Under high-temperature conditions (>600°C), radiation efficiency is related to the thermal expansion coefficient of the substrate. Pre-testing is required.
(3)The mixed two-component coating must be used within 12 hours. Tools should be cleaned promptly to prevent curing.
(4)Operators should wear protective gloves, masks, goggles, etc., to avoid direct skin contact with the coating.
(5)After application, promptly clean tools and equipment with a dedicated solvent.
3. Application Parameters
Parameter | Value | Parameter | Value |
Coating Solid Content (%) | 75-85 | Curing Temperature (°C) | 180-250 |
Theoretical Coverage (m²/kg) | 8-12 | Curing Time (h) | 1 |
Dry Film Thickness (μm) | 20-30 | Instantaneous Temperature Resistance (°C) | 1000 |
Pot Life (h) | 12 | Recommended Operating Temperature (°C) | -30 to 800 |
Thinner | Alkanes, Esters | Flash Point (°C) | <22 |
4. Storage and Safety
Storage Temperature | 5°C-30°C, cool and ventilated, away from fire sources. |
Shelf Life | 6 months (unopened). If expired, re-inspect and use only if qualified. |
* Dispose of waste coating according to local environmental regulations.